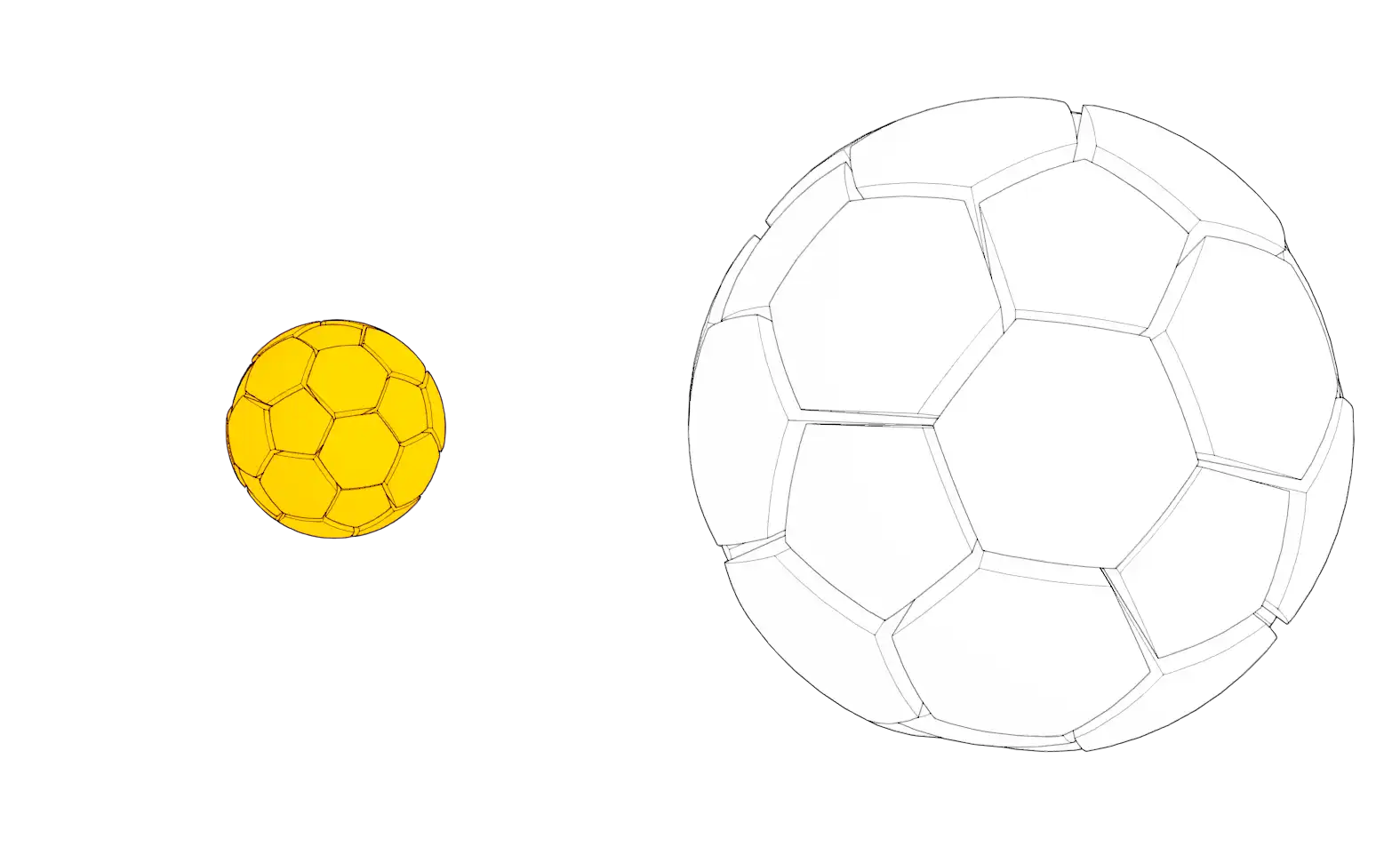
Solutions for Terrible Micro Reactor Burnup
Designing a reactor core barely half a meter wide sounds simple—until you start counting neutrons. Here’s a quick tour of the roadblocks that keep most “trash-can” reactors on the drawing board—and the new tricks to beat them.
The key challenge is cost
Tiny cores used in micro reactors have terrible fuel utilization. TRISO fuel can be burned to generate 160 MWd/kg (energy/mass), but many of these transportable reactor concepts will have burnups in the 1–20 MWd/kg range. TRISO is already a very expensive fuel, roughly 10–20× normal nuclear fuel at the same enrichment. At these high costs and the low burnups of a micro reactor, the fuel is barely used and ends up costing similar to or more than diesel.
The figure below uses the data produced for the Neutronics Scoping Tool to chart out LWR and HTGR burnups at different radii and enrichments. The first row shows the burnup (higher is better up to the fuel's burnup limit), and the second row shows the fuel's cost in cents per kWh (money/energy). Blue lines are for LWR and green lines are for HTGR. Each line is a different enrichment. The orange band shows diesel costs.
The calculations assume standard core designs and materials. This is an overall lower bound on the burn. But the model does not include temperature effects that would reduce burnup.
It's pretty clear that small cores get really expensive. Enrichment helps, but only for HTGRs. Higher enrichment up to 20% helps HTGRs since TRISO fuel can achieve the very high burnups required. LWRs can lower fuel costs with up to 5% enrichment since LWR fuel pellets but higher enirchments than that are basically useless since the LWR fuel pellets and cladding cannot withstand much beyond 60 MWd/kg.
To fit in a standard container with an acceptable level of shielding, the maximum core diameter is probably about 100 cm. Tiny LWR cores can be done without a huge hit on fuel costs because of the highly efficient water moderator and the LWR fuel is very inexpensive to start with. But HTGR gets absolutely hammered because of the high cost of TRISO and the terrible volume efficiency of graphite. The minimum viable core diameter at 20% enrichment is probably around 200 cm. Lower enrichments require larger cores for the same fuel cost.
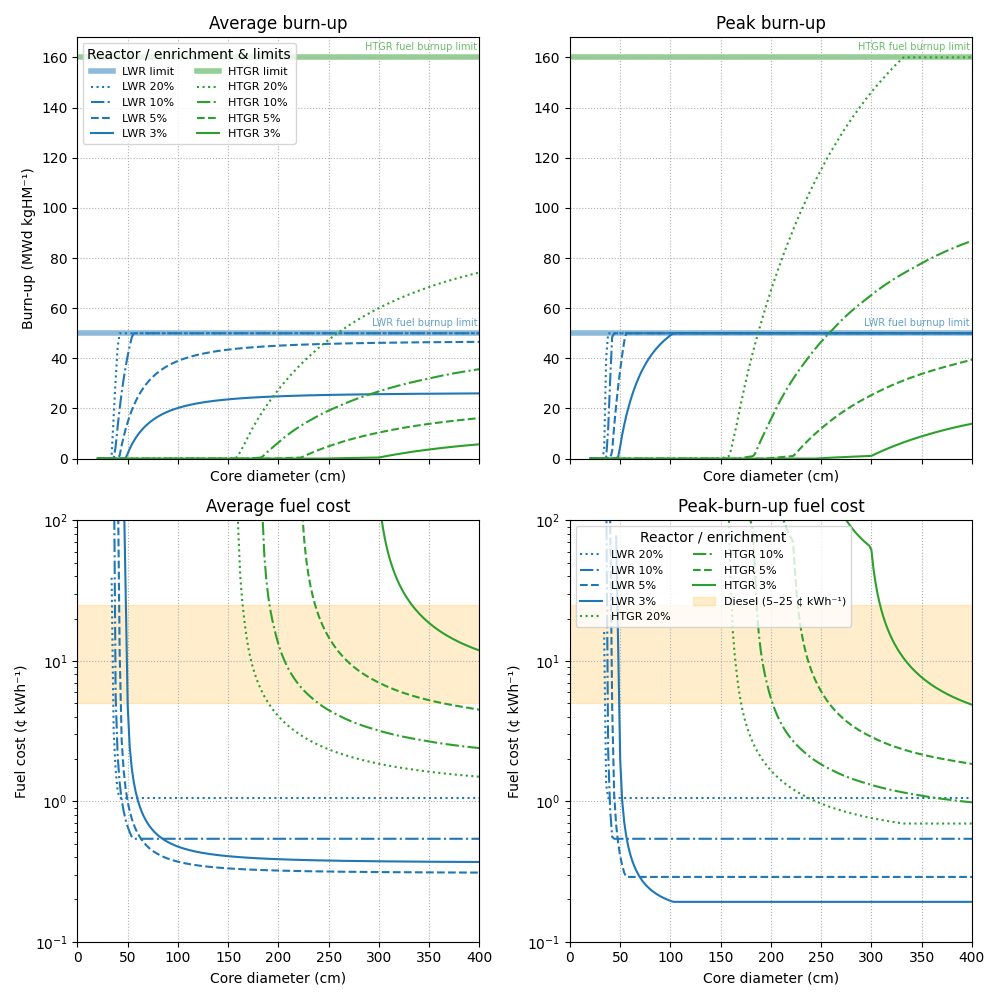
In practical terms, why do micro reactor cores have such terrible burnup?
1. Criticality needs a minimum fuel mass
A core must achieve criticality (self-sustaining neutron population), and this requires a minimum amount of fuel—the critical mass. Even the cleverest designers can’t cheat physics: there’s a critical mass of fissile material you simply have to load.
2. Civilian enrichment caps add bulk
International safeguards limit commercial uranium to < 20% U-235. To stay below 20% enrichment uranium, as basically required by all international nuclear agreements for civilian power, you have to add more fuel, which quickly balloons core size.
3. Fuel isn’t 100% fuel
If you are using TRISO particle fuel, you'll end up wasting quite a bit of volume on filler material between the fuel particles as well as the ceramic protective layers on the particles themselves. For TRISO, the uranium-bearing kernel is just 12% of the particle volume, and the particles are at most 50% of the fuel pellet (cylinder) volume. Even if not using TRISO particle fuel, space is wasted on metal claddings and other structural materials. More fuel needed.
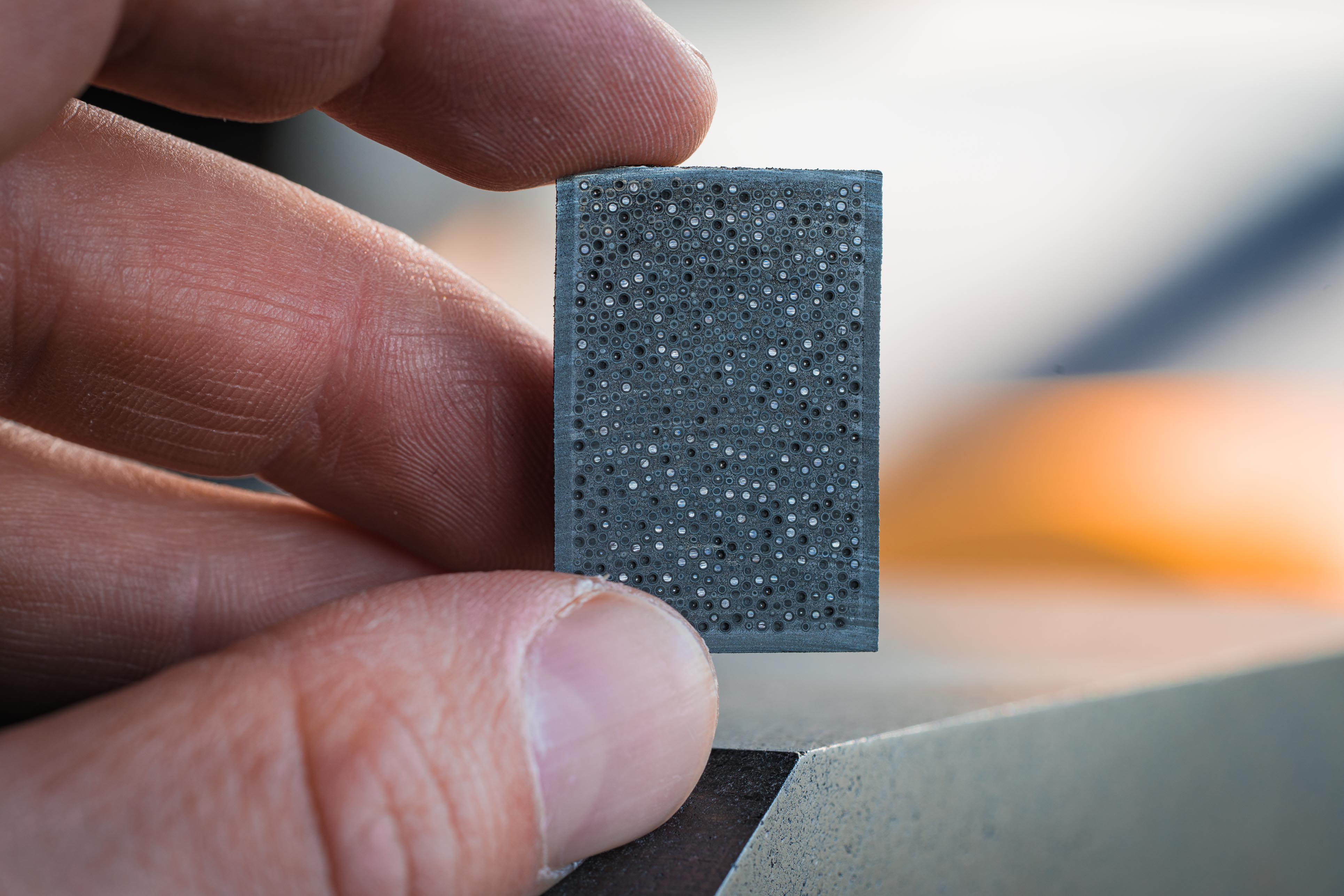
4. Moderators eat volume
To efficiently use and burn up the fuel, you would like a large core size (less surface to leak neutrons) with more moderator (non-fuel material like graphite or water used to shape the neutron spectrum and improve neutron utilization), and most moderators use up a bunch of space, roughly 10–20× more than the fuel itself. The core is getting big!
If you shrink the diameter, the surface-area penalty grows, forcing still more moderator.
5. Coolant channels take another bite
You need to add coolant channels to extract heat from the hot core, and these consume quite a bit of volume. It's about 5% for a reactor like the USNC MMR, and ~35% for pebble bed reactors like the one below. Big waste of space.
6. The “Navy fix” isn’t great for civilians
The go-to method used by the US Navy is to use high enrichment fuel and water moderator. The water moderator serves as both moderator and coolant. Not bad, but also not a great option for civilian reactors with commercial goals and high temperature aspirations.
High enrichment with low burnup is not a great tradeoff. Most micro reactor concepts have terrible fuel efficiency, far worse than existing nuclear power plants, to the point that the nuclear fuel cost starts to dominate. So increasing enrichment without efficiently burning it is a losing game.
The Compact-Core Playbook
But there are tricks and approaches to reduce every penalty above using optimized geometry, advanced moderators, and clever operational tricks.
Core topology optimization
Reactor core geometries can be optimized to improve the burnup. Designers tune parameters like fuel pellet diameter, fuel spacing, enrichment and they sometimes vary these parameters across the core to achieve maximal burnup. Its crucial for these estimates to include heat transfer effects as temperature has a significant effect on total burnup. Optimal design varies with reactor size, materials, coolant, coolant channel needs, and the details of the fuel including the enrichment and packing density. There are some pretty non-obvious trends in core design for micro reactors that allow for enhanced burnup beyond what was shown in the figure at the start of the post.
A new opportunity in the next decade or two is the use of additive manufacturing. New techniques can produce non-standard fuel geometries to accommodate complex two-pass coolant pathways in the core while maximizing fuel loading and minimizing thermal stresses in the fuel. This is can be integrated with advanced moderators (Fuel Moderator Inversion Blocks). The best part is that new shapes and form factors can be produced with the same tooling at almost no extra cost.
Additive manufacturing is only as useful as the designer can make it. Nuclear core design can have many objectives. Design usually aims to minimize size and fuel temperature to get the highest overall burnup. USNC has developed RAPTOR, a code that can efficiently evaluate variations of nuclear core designs using state-of-the-art physics code tools like MCNP, SERPENT, MOOSE, etc. Together with AI optimizing techniques and topology optimization, one can design and additively manufacture novel geometries that improve fuel utilization without new tooling. In this way, new concepts are emerging in nuclear core design including in-vessel shielding, new heterogeneous geometries, and inverted moderators.
Hydride Moderators
Swapping out the graphite moderator for a hydride moderator can significantly improve burnup for the same core size. Hydride moderators are simply hydrogen-containing materials that can be used to moderate neutrons in nuclear reactors. They are extremely effective neutron moderators that allow reactor cores to be small—without using high enrichment fuel. Think trash can sized.
Zirconium hydride (ZrHx), yttrium hydride (YHx), and H2O are the three most promising moderator materials in terms of the moderating ratio, which is the ratio of the macroscopic slowing-down power (the product of the average logarithmic energy loss per collision and the macroscopic neutron scattering cross section) to the macroscopic cross section for neutron absorption. Although H2O has been used in nuclear reactors since the beginning of the industry, both as coolant and moderator, its application as a high temperature (>400 °C) moderator material is restricted by the requirement for extremely high pressure.
But ZrHx and YHx can be used at high temperatures and could be used for gas-cooled reactors (like MMR) to reduce the size of the core or increase the fuel utilization (efficiency). It was used over 50 years ago in the Systems Nuclear Auxiliary Power (SNAP) Program, TRIGA, and nuclear thermal propulsion programs, and many vendors are bringing it back. The size reduction can be significant.
Yttrium used to be an extremely expensive powder, but is now widely available at an affordable price, even at the ultra high-purity grade of 99.9%, which is <$5\0/kg. Reactors can significantly benefit from smaller size and increased fuel efficiency from using a metal hydride.
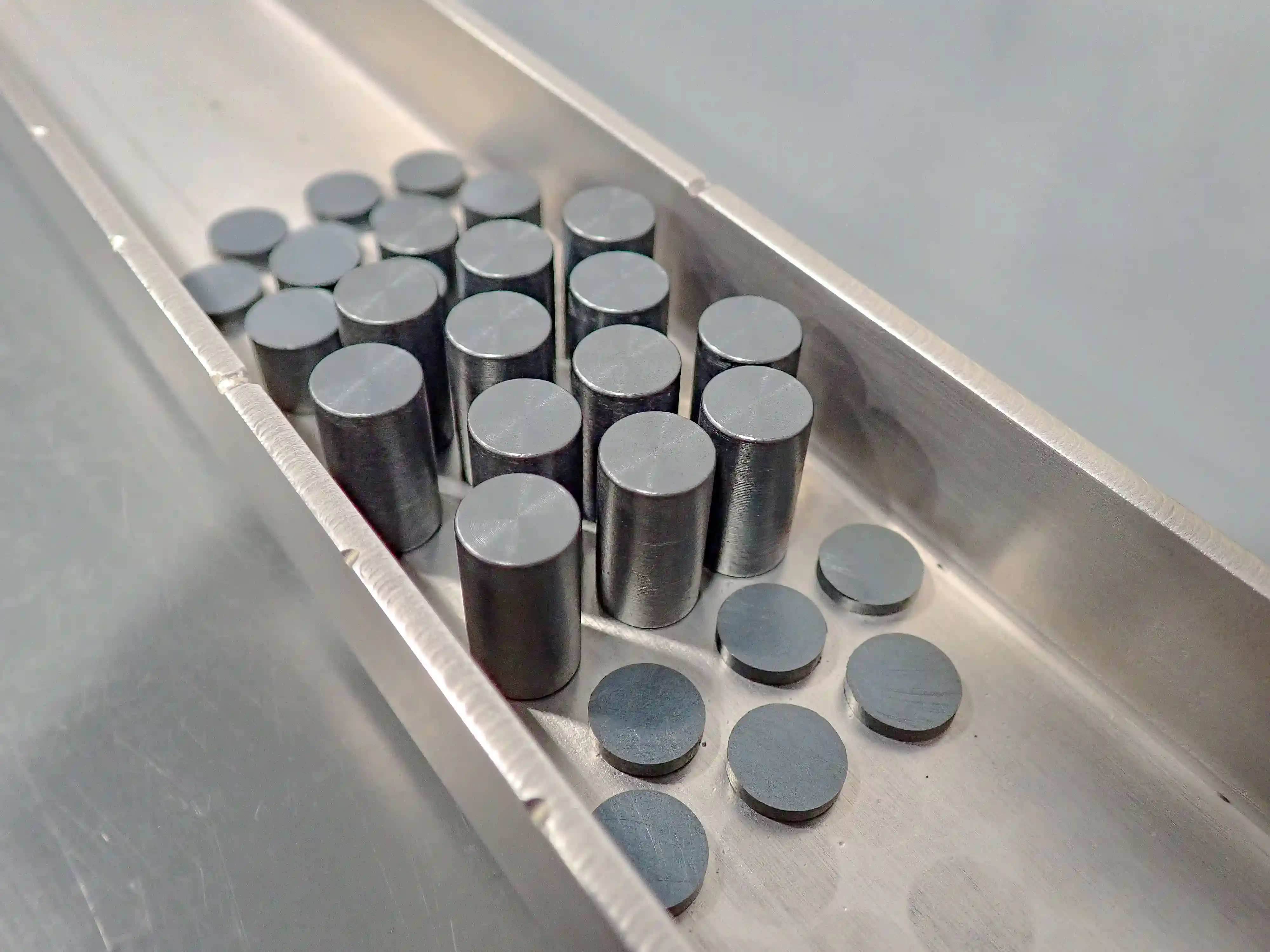
Hydride fabrication challenges
There are two main challenges in the fabrication of hydride moderators. The first is the production of bulk yttrium hydride in large-scale, crack-free, bulk form. Yttrium and zirconium love hydrogen, and will destroy themselves as they absorb it. To make robust metal hydrides that don't pulverize or crack themselves, we have to very carefully control the temperatures and pressures as we hydride the metal both in the uptake and cool down. USNC does all the hydrating in house with extremely specialized furnaces and equipment.
Until 2020, it had not been demonstrated for nearly a half-century. In the new process, we avoid the use of powders and compaction that introduce impurities and voids. For nuclear reactors, the materials must be kept highly pure and free of voids. USNC developed processes and integrated techniques from ORNL to create fully dense, monolithic hydrides with precise hydrogen ratios. They are crack free and extremely high quality. Problem 1 is mostly solved.
The second problem is hydrogen escape. As temperatures increase, hydrogen desorbs from the material as a gas, and escapes. Hydrogen barriers must be added, such as coatings or pressure vessels. Adding barriers is challenging because temperatures must remain low during the manufacturing process to ensure hydrogen does not desorb. If the temperatures are elevated, all the hydrogen escapes as you make the barrier and the component is useless. We've developed three containment approaches. In the first, hydrides are sealed in steel cans. This is effective up to a point. We don't usually like using metals inside the reactor core, owing to temperature limitations and water/air interactions. In the second method, we place the hydrides in a SiC can, creating a gas-tight ceramic barrier. This allows the hydride component to be used at very high temperatures without any loss of hydrogen and it protects the hydride from other chemicals and components.
The final method for hydride containment is a composite moderator in which we use similar techniques as in our fuel fabrication to create particles of hydride in a silicon carbide matrix. Problem 2 is solved, and now we can deliver canned hydrides for the entire community of micro reactor developers. We welcome applications from reactor vendors, no matter how small.
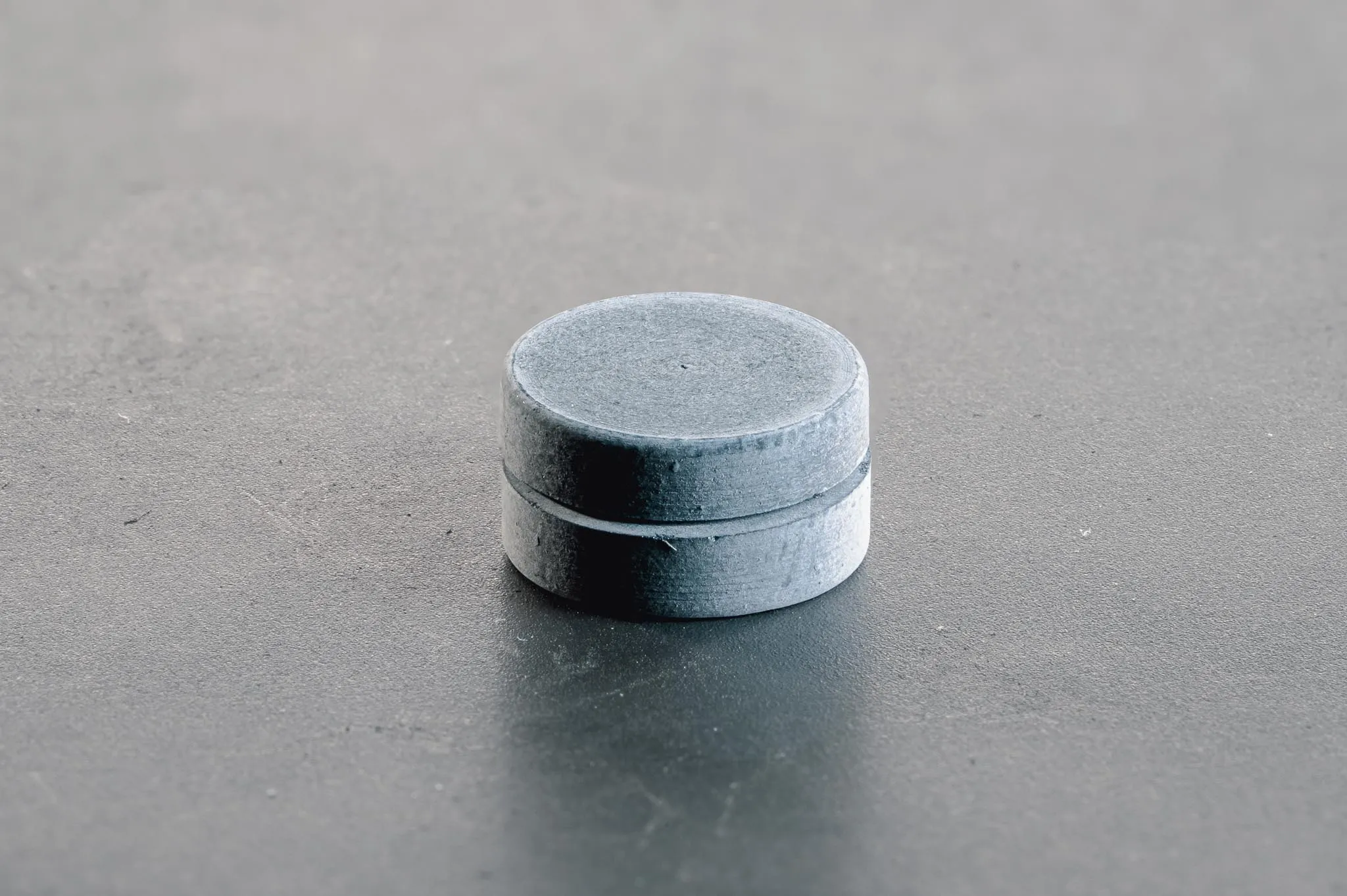
Fuel reshuffling
Fuel reshuffling is already common practice in LWRs to maximize energy extraction from the fuel pellets and provides core balancing to reduce hotspots. Every two years or so, the reactor shuts down for refueling. But only the fully burned fuel is extracted and replaced with fresh fuel. The rest of the fuel stays in the reactor and is moved around to maximize the burnup.
The same approach can be taken with micro reactors to increase burnup, but the challenge is fuel handling facilities in the field would be expensive due to low utilization.
Two Reactor Fleet
(---)
Conclusion
Fuel costs for micro reactors are high, but there are good avenues to reduce them.
- Advanced hydride moderators: Using high-purity yttrium and zirconium hydrides as neutron moderators, with specialized fabrication and containment methods to prevent cracking and hydrogen loss.
- Fuel reshuffling: Adopting fuel reshuffling practices from large reactors to maximize fuel utilization, though field implementation is challenging for micro reactors.
- Central deep burner with dispersed light burners: Deploying many small reactors for partial fuel use, then sending the used fuel to a central large reactor for complete burnup, especially suited for robust TRISO fuel.
- Core topology optimization: Leveraging additive manufacturing and AI-driven design tools to create novel core geometries and fuel arrangements that enhance burnup and reduce size, without the need for new tooling.
Cost-effective “trash-can” reactors may actually turn out to be practical, economical power sources.