How Nuclear Fuel Fails
The general public and even most nuclear engineers do not understand how easy it is for nuclear fuel to fail. Since the dawn of the nuclear era, nuclear fuels have been designed and built to meet only a small portion of the full requirements. This was due to material and technology limitations as well as costs. The only economical and practical way to use nuclear material for power has been simple fuel oxide pellets in metal cans.
That is now changing with the introduction of TRISO particle based fuels and use of advanced radiation tolerant ceramics. In this post, I will explain the performance goals of nuclear fuel and then show how normal fuels compare relative to TRISO based fuels.
Still there's a limit to what I can do with words. I can write all about nuclear accidents and the performance characteristics of traditional fuel compared to new TRISO-based fuels, but people often don't get it. The technical discussion of materials in nuclear reactors and how they affect fuel performance is not straightforward. But the practical differences between traditional and TRISO-based fuels would be plainly obvious if we could observe the fuel forms in action. We can't visually observe nuclear accidents as cameras can't survive the radiation, but we can show what happens using animations. So I rigged up a quick animation showing how traditional fuel and TRISO/FCM fuel look like as they encounter the same or similar conditions. I've made simplifications for the sake of comparison and illustration, but the general idea stands that during severe accidents, traditional fuel will fail to the point of melting and vaporization while TRISO/FCM fuel remains solid and functional.
Nuclear Fuel Goals
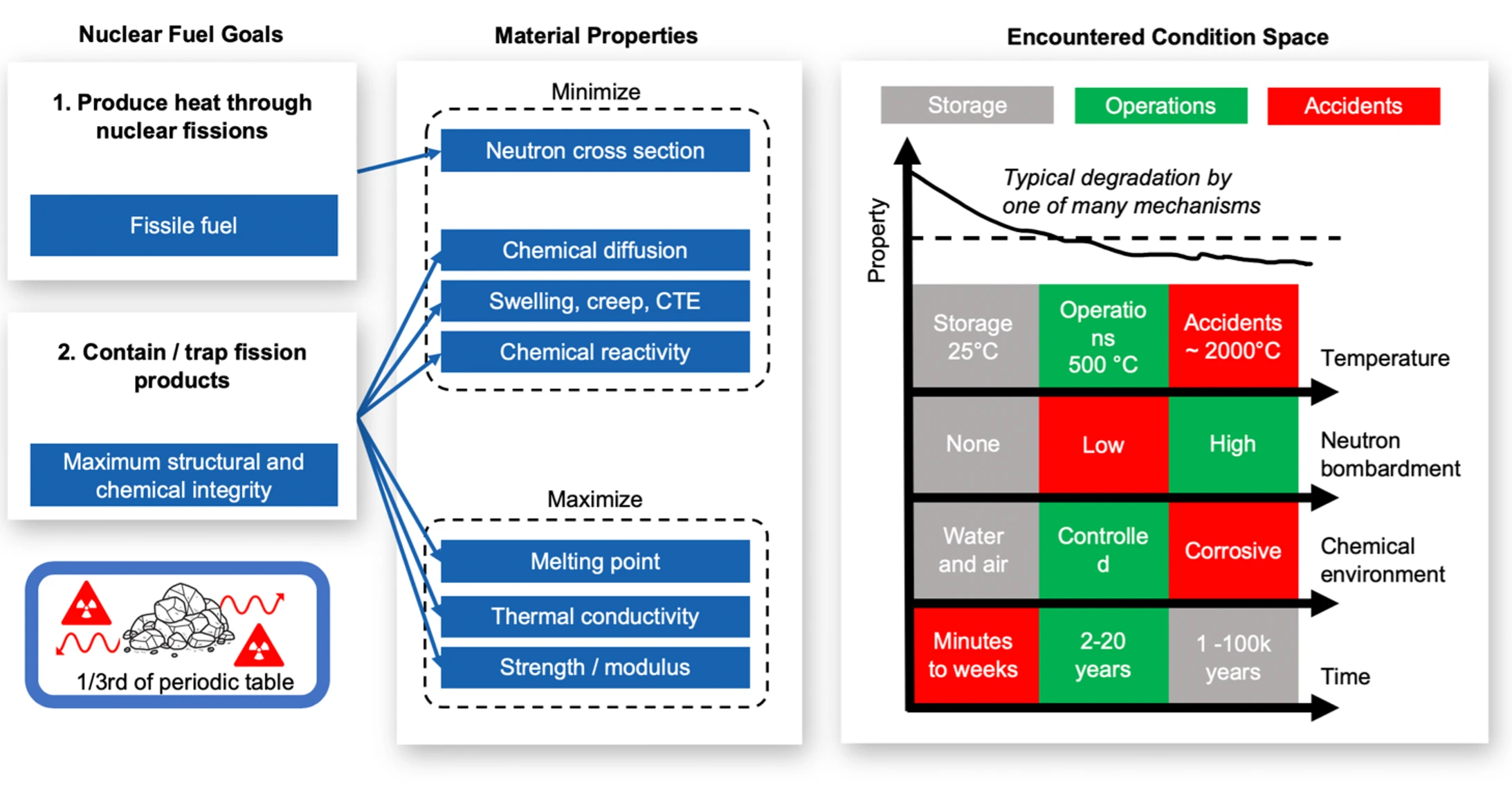
Figure 1 illustrates nuclear fuel's performance goals and the properties needed to achieve those goals. The first goal of nuclear fuel is to generate heat from fission reactions. This is done by placing enough fissile fuel, usually U-235, close together to achieve a critical configuration. Besides having Uranium somewhere in the fuel, the other materials should not interfere with the nuclear reactions. In other words, the materials should not absorb neutrons. This means the thermal neutron cross section must be minimized which limits the material selection to perhaps less than a dozen elements including O, C, Mg, Be, Si, Zr, Al.1
Now, as the fission reactions take place, the Uranium is slowly turning into roughly one third of the periodic table as solids and gases. These are the fission products that make nuclear dangerous, and they must be contained for they are radioactive and corrosive. So beyond generating fission heat, the fuel needs to contain and trap the fission products in place. To do that, the fuel must have good structural and chemical integrity, and it must maintain its integrity across the encountered conditions. These conditions fall into roughly three categories: power producing operations, worst case accidents, and long-term storage. Each category has characteristic temperature and radiation ranges.
Figure 1 shows relatively large parameter swaths and is a simplification of possible fuel conditions meant for illustrative purposes. In the language of nuclear engineering, the term "accidents" means beyond-design-basis accidents. Standard operating temperatures for the fuel in a reactor may be in the 400 to 700 °C range depending on the reactor type, with high neutron bombardment, in the presence of fission products and coolant, and with exposures lasting 2 to 20 years. Accident conditions might involve temperatures in excess of 1000°C for minutes or weeks. Storage conditions are relatively benign with reasonable humidity and temperatures, but materials may need to endure for thousands or tens of thousands of years.
Generally, the material selection should aim to minimize properties like diffusion of fission products, chemical activity with air and water (since that is what we encounter on Earth's surface), thermal expansion, and swelling. We seek to maximize properties like melting temperature, thermal conductivity, strength, hardness, and modulus. The properties have to be good enough across the encountered conditions which span temperature, neutron bombardment (or displacements per atom), chemical environment, stress, and time. Degradation occurs by various mechanisms like swelling, irradiation and chemical embrittlement, segregation, micro-structural change, and transmutation.2
The Top-Down Approach
The fuel used in today's water-cooled reactors, which make up about 99% of reactors worldwide, is uranium oxide fuel in metal cans. Call it canned fuel. It is designed only for standard operating conditions and very low-key accidents: essentially the green portions of the condition space in Figure 1. This fuel is just Uranium dioxide pellets that crumble and outgas inside a Zircalloy cladding (How it's made), or pressure tube, as shown in the left panel of Figure 2. During operation, the pellets swell, crack and crumble, but remain well confined inside the tube. Sometimes, Zircalloy cans rupture releasing fission gases into the coolant which happens at a rate of about 1 per 500,000 fuel cans per year.3 A typical water-cooled reactor has about 1 million fuel cans, so this happens on average every year at every reactor. It's just one rod failure, and the coolant is already radioactive. This is annoying but manageable.
This becomes unmanageable when multiple fuel cans fail, which usually occurs during accident conditions where corrosion, melting, and hydrogen explosions lead to coolant loss, containment failure and release of fission products. If the things fail nicely, the concrete containment will keep most of the radiation from reaching the atmosphere. Like at the Three Mile Island, the power plant would be trashed and the government will foot the cleanup costs, but the public is protected. If things fail in unexpected ways like at Fukushima, spent fuel pools and containments can fail and fission products can be released to the environment.4 Traditional nuclear fuel is the Achilles heel of nuclear reactors.
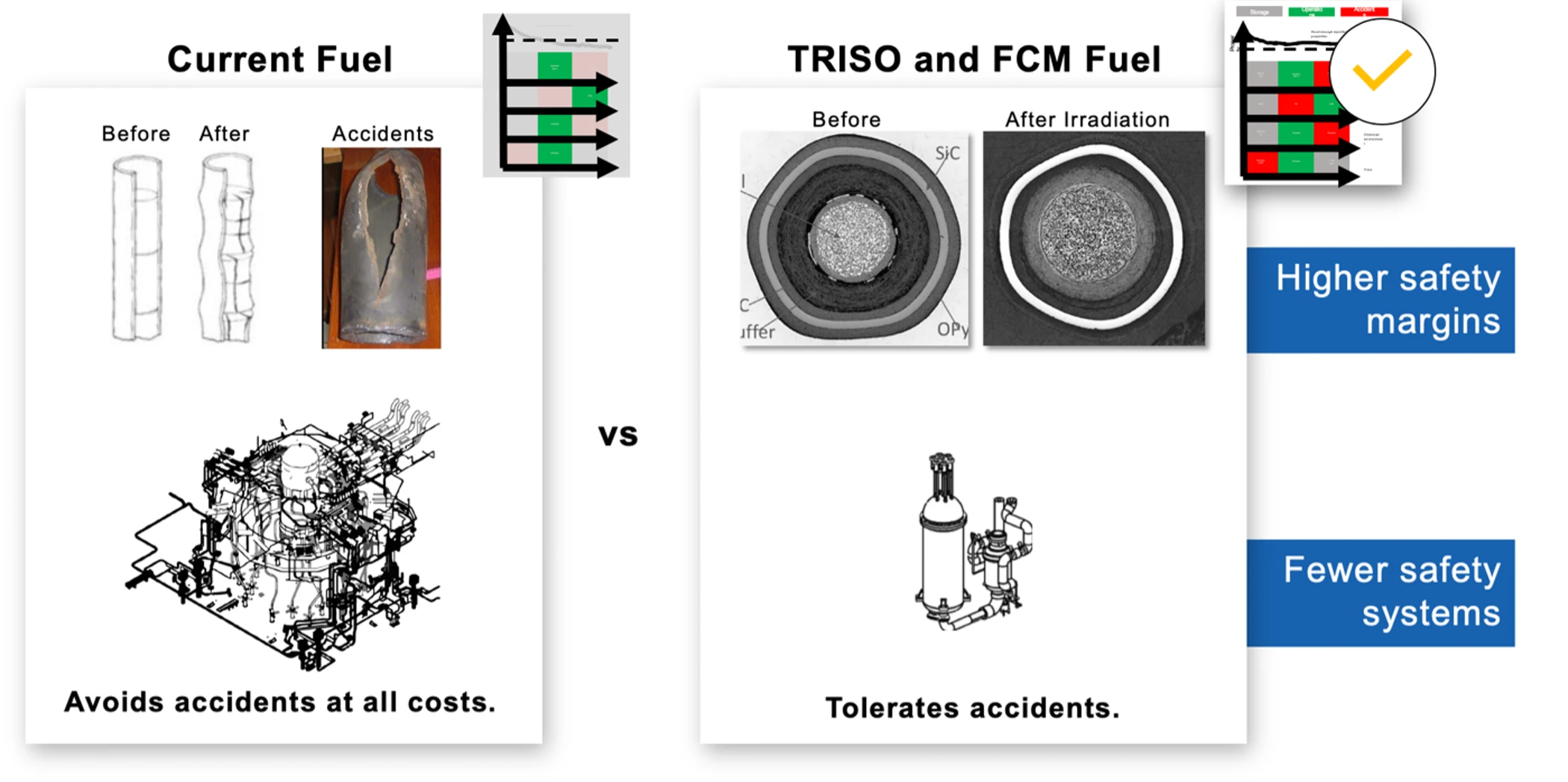
Figure 2 shows traditional/current fuel used in power producing reactors compared to TRISO/FCM fuel in terms of accident tolerance, safety margins, and system complexity. Targeted condition space for each fuel designed is shown in the top right. The top of each panel shows the fuel's appearance before and after irradiation. The bottom of each panel shows the likely effects on final design and complexity of the power plant are inferred in the sketches which show a traditional light water reactor in the left panel and the USNC MMR in the right panel.
To hide the Achilles heel, reactors have to "avoid accidents at all costs." Needless to say, the costs balloon rapidly. Accident probabilities are lowered by adding safety systems with extra redundancy and truckloads of extra paperwork. Since failures still occur and no one believes the probabilities, the reactor is fortified to try to contain accidents and reduce the public's radiation exposure. These systems also fail with some probability. The final result is an intricate fortress with complex and high quality safety systems that is expensive to build, operate, and maintain. And despite best efforts, this approach still leads to expensive accidents like Three Mile Island or Fukushima. There are pictures of the Elephant's Foot at Chernobyl, but we don't yet have pictures of the Three Mile Island melted core. The below image is probably what it looks like.
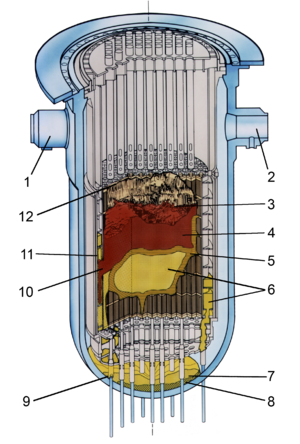
This is the top down approach for fuel and safety, whereby the radiation problem is mitigated by spending more money and adding extra and higher layers of engineering systems. This is usually the most inelegant and most expensive way to build an engineering system. I view these designs as highly impressive and technically competent designs, but misguided from the beginning, a bit of a Rube Goldberg approach.
Why is everyone still designing and building reactors in this top-down approach? Because it's easy from a project management and risk perspective. It's easy to hire an established engineering firm to design engineering systems around the reactor. It's easier to convince a banker to finance something similar to existing systems. It's easy to stick to the old methods and approaches that have established feasibility and costs. It's easy to comply with the existing regulatory system. It's easy not to innovate.
The Bottom-Up Approach
We have to carefully pick where to do the engineering and where to concentrate our efforts. The bottom-up approach is to engineer solutions at the source of the problem – the fission products. One way would be to avoid the fission products and radiation altogether, which unfortunately is not an option if we want to generate nuclear heat. The other way is to make high performance fuel. The idea is to spend money and effort at the lowest level of the fission product hierarchy - the location where fission products are made, the root cause. This prevents the problem from growing in size and scope, precluding the need for more complex and expensive solutions at higher levels of the hierarchy such as the cladding, the pressure vessel, and the containment.
This approach embraces the fact that accident conditions occur, accepting that they will happen at some point. And then designing the reactor and fuel so that the worst-case accident is a tolerable ordeal. To do that, the fuel must be designed to meet all the performance requirements. The fuel's properties must be good enough across the encountered conditions shown in Figure 1, rather than only the operating conditions.
TRISO particle fuel, and in particular its augmentation in FCM fuel, is shaping up to be just such a fuel. The irradiated fuel is largely indistinguishable from the virgin fuel. This is primarily achieved by using high temperature ceramics like graphite and silicon carbide to create tiny spherical pressure vessels called TRISO particles. These ceramics have excellent performance in terms of fission-gas retention and radiation tolerance. They also have excellent thermal conductivity and high melting points. For more on TRISO, see my previous post.
Why are these new fuels being deployed now? SiC has long been known to be an incredible material for nuclear applications, with excellent properties that withstand high temperatures and extreme radiation. But using it effectively in engineered systems has been challenging due to knowledge gaps and manufacturing capabilities.
Over the last several decades, SiC's performance characterization has been fulfilled . And most recently, the manufacturing challenges have been solved with feedstock and manufacturing costs coming down dramatically. The other major driver for these advanced fuels is that people don't want traditional reactors and traditional nuclear fuel. Calls for a better approach to safety have driven the R&D and commercial deployment of these robust and accident tolerant fuels.
What's happening in the animation?
Normal Fuel fractures, ruptures, and melts
Traditional fuel here is shown as UO2 pellets in Zircalloy cladding (metal tube). But similar melting and fission product release would occur for metal fuels. For traditional fuel, the pellets will experience radiation induced swelling of about 30% and fracture into chunks. The UO2 will also experience columnar grain growth that looks a bit like needles, but I this isn't shown in the animation. The expanding pellets will rub up against the cladding and fission product gases are released inside the cladding where pressure is building up. This is all expected during normal operations.
Initial problems occur if the pellets expand a little too much or if the Zircalloy cladding isn't quite within tolerance. In this case the clad will form a ribbed structure that presents weak points where the clad is likely to fail. When the fission gas pressure inside the clad exceeds the limits, the clad will rupture like an exploding soda can.
An alternative way for the clad to fail is corrosion or melting. When temperatures rise, water and the Zirconium in the cladding start to react to form hydrogen gas. The cladding will quickly weaken until it ruptures or crumbles, again, releasing the fission products. If temperatures go above roughly 1800 °C, the clad will melt. Why might temperatures rise? Temperatures can rise very quickly in a nuclear reactor when coolant slows down or stops flowing. This can happen if the the coolant leaks out of the reactor, if the pumps stop working, or if the coolant channels get clogged. Temperatures could also rise if control rods are withdrawn inappropriately. Here's a video of experimental conditions where temperatures rise dramatically.
At this point, the fuel form has already failed because all the fission gases are now released into the coolant. If you're lucky, the coolant is still restrained within the reactor pressure vessel. But this could happen in the spent fuel pool which does not have a pressurized boundary or containment. Even in the reactor, it's quite likely that hydrogen gas generation or other abnormal conditions have led to an explosion or the coolant has leaked into the containment. Now you are hoping that the concrete containment structure is functional and that the chemical sprays used to capture volatile fission products are operating as planned. Not a fun place to be.
Even if everything goes according to plan in the reactor, this fuel is not ideal for long term storage. For starters, the fuel is hot when it comes out of the reactor, so it has to be placed in a big pool of circulating water for a few years. This is called wet storage and requires a large 12 m deep pool and must avoid leaking or loss of circulation to prevent fuel failures. Thereafter, it must be transferred to dry storage and ultimately placed in specialized containers for long term storage in geologic repositories.
TRISO/FCM Fuel just sits there
The SiC material that binds together the TRISO particles is extremely stable under irradiation and melts at around 2800 °C. There is no cracking or swelling and the material properties equilibrate to adequate levels. The TRISO particles inside the fuel contain the more than 100 MPa fission gas pressures and are aided by the SiC ceramic matrix.
After use, TRISO/FCM fuel does not require wet-storage. It's expected that it can be placed in a geologic repository pretty much as is. The SiC matrix is unreactive with air and water so the repository could even suffer from air flow and water flooding without a significant risk of radioactivity release. These fuel forms can be expected to have million year stability, far more than the 10-100 thousand years needed to reach negligible radiation levels.
Why are these claims reasonable? Because we humans have done it before, with less performative ceramics and in far worse conditions. Look no further than the intact greek and roman amphoras found lying at the bottom of the Mediterranean Sea, still filled with 3000 year-old wine and garum.